KEWEI Steps of Investment Casting
Precision Engineering for Complex Metal Components
Introduction
Investment casting, also known as the lost wax process, is a centuries-old technique refined for modern precision manufacturing. As a global leader in advanced foundry solutions, KEWEI combines cutting-edge technology with decades of expertise to optimize every step of investment casting. This guide explores the 7 critical steps of investment casting, highlighting how KEWEI’s innovations empower aerospace, medical, and automotive industries to achieve flawless results.
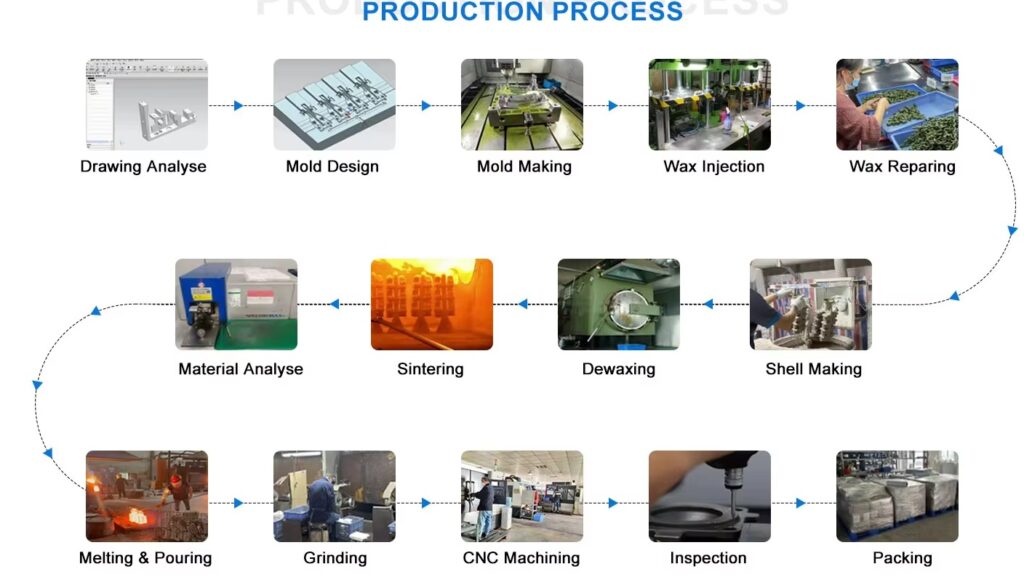
1.Investment Casting Step 1: Wax Pattern Creation
The process begins with crafting precise wax replicas of the final part. KEWEI’s solutions include:
- 3D Wax Printing: Achieve ±0.05mm accuracy for complex geometries (e.g., turbine blades).
- AI-Controlled Wax Injectors: Reduce defects by 35% through real-time temperature and pressure adjustments.
KEWEI Innovation: Proprietary low-shrinkage wax blends ensure dimensional stability.
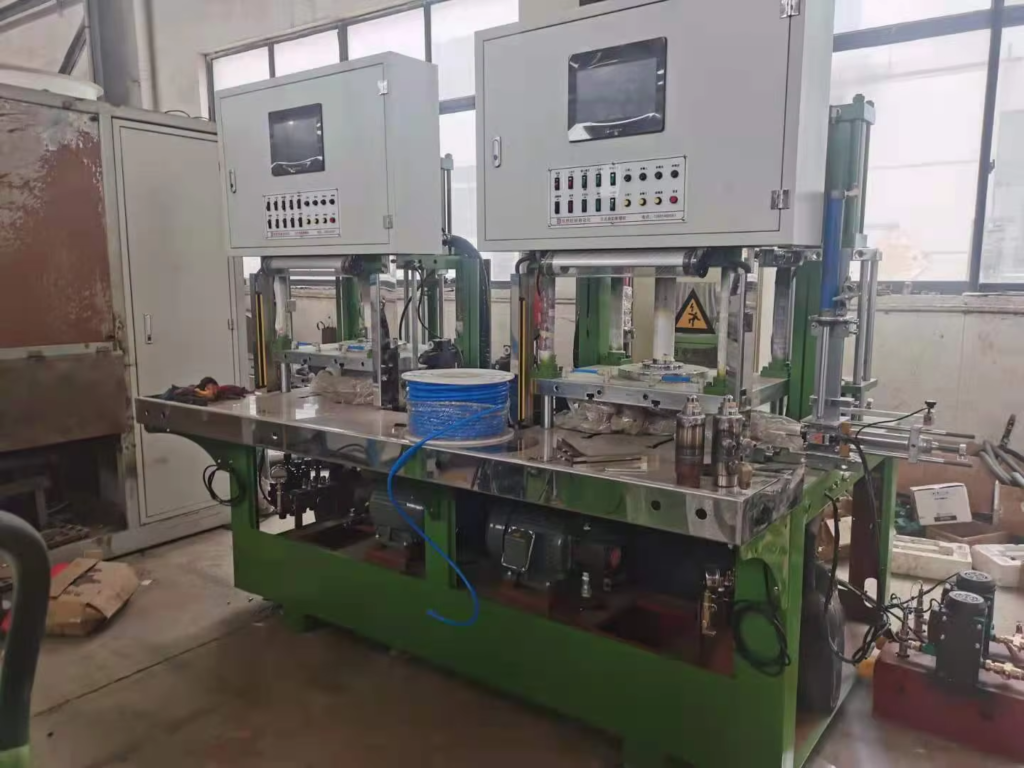
2. Investment Casting Step 2: Assembly of Wax Clusters
Multiple wax patterns are attached to a central gating system. KEWEI enhances efficiency with:
- Robotic Assembly Arms: Assemble clusters 50% faster than manual methods.
- Modular Gating Design: Optimize metal flow and reduce material waste by 20%.
Fully automatic shell making system
3.Investment Casting Step 3: Ceramic Shell Building
A ceramic shell is built around the wax cluster through repeated dipping and stuccoing. KEWEI’s technology excels with:
- Automated Slurry Coaters: 6-axis robots ensure ±0.1mm shell uniformity.
- AI-Driven Drying Tunnels: Cut curing time by 30% with predictive humidity control.
Case Study: A turbine blade manufacturer reduced shell cracking by 90% using KEWEI’s zircon-based ceramic slurry.
4.Investment Casting Step 4: Dewaxing
The wax is melted out of the ceramic shell in a high-temperature autoclave. KEWEI’s systems feature:
- Rapid Dewaxing Cycles: Complete in <15 minutes vs. traditional 1-hour processes.
- Wax Recycling: Reclaim 95% of wax for reuse, cutting material costs.
Dewaxing Kettle for Investment Casting
5.Investment Casting Step 5: Metal Pouring
Molten metal is poured into the preheated ceramic mold. KEWEI’s advancements include:
- Vacuum Induction Furnaces: Melt superalloys (Inconel, titanium) up to 1800°C with ±3°C stability.
- IoT-Enabled Tilt Pouring: Eliminate turbulence-induced porosity in thin-wall castings.
Investment Casting Pouring robot
6.Investment Casting Step 6: Shell Removal & Finishing
The ceramic shell is mechanically removed, and the casting is finished. KEWEI optimizes this stage with:
- Automated Knockout Systems: Remove shells 50% faster without damaging parts.
- 5-Axis CNC Machines: Achieve Ra <0.8μm surface finishes for medical implants.
Shell knockout machine for investment castinhg
7. Investment CastingStep 7: Heat Treatment & Inspection
Final heat treatment enhances mechanical properties, followed by rigorous quality checks. KEWEI delivers:
- Vacuum Heat Treating Furnaces: Ensure ±5°C uniformity for aerospace alloys (AMS 2750 compliant).
- AI-Powered Inspection: Detect micron-level defects with 99.9% accuracy.
Related Keywords: investment casting process steps, precision lost wax casting
Why Choose KEWEI for Investment Casting?
- End-to-End Expertise: Master all steps of investment casting with integrated solutions.
- Smart Factory Ready: IoT and AI optimize every stage for speed, cost, and quality.
- Global Compliance: Meet AS9100 (aerospace), ISO 13485 (medical), and IATF 16949 (automotive).
Conclusion
Mastering the steps of investment casting requires precision technology and deep industry knowledge. With KEWEI’s 20+ years of innovation, 50+ patents, and client-centric approach, manufacturers transform raw materials into high-value components—flawlessly and efficiently.
Ready to Optimize Your Casting Process?
Contact KEWEI for a Free Process Audit!