Automatic Core Shooter
The automatic core shooter Coated Sand Core Shooting Machine uses coated sand as the raw material and operates on the hot core box principle to produce coated sand molds. The core shooting process uses phenolic resin sand, which results in high production efficiency, precise dimensions, smooth surfaces, and the ability to produce castings with complex inner cavities.
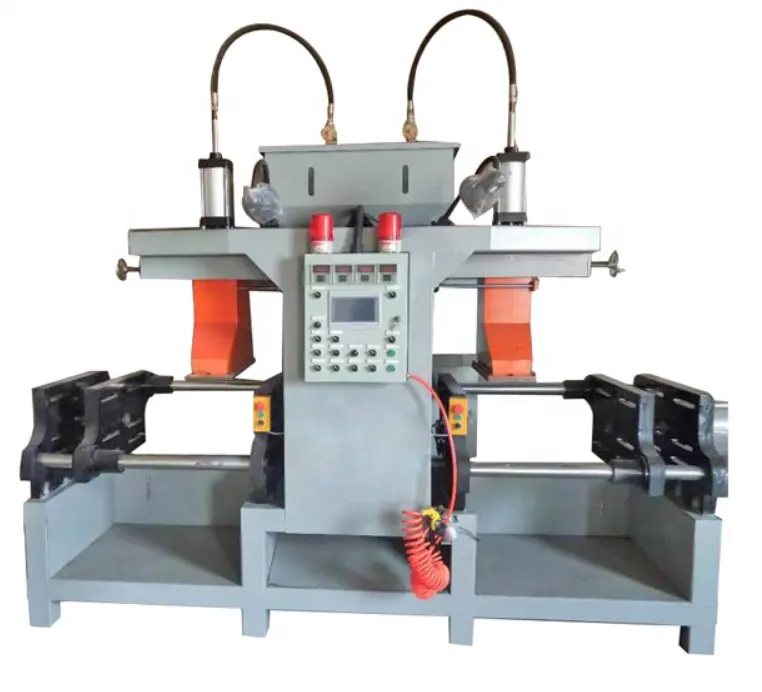
Technical Specifications and Key Advantages of ZH650 Double-Head Core-Shooting Machine
I. Equipment Overview
Item | Specification/Configuration | Comparison with Traditional Equipment |
---|---|---|
Application | Shell molds & shell cores production | Single-head machines limited to one mold type |
Control System | PLC programmable control (supports recipe storage/recall) | Manual/semi-auto adjustment, unstable parameters |
Cycle Time | 30–240 sec (mold size-dependent, ±5% adjustable) | Fixed cycle, low compatibility |
Sand Shooting Pressure | 0.4–0.7 MPa (high-pressure airflow injection) | Typically ≤0.5 MPa, uneven filling |
Mold Temperature Control | Dual-mode heating (electric/gas) with closed-loop control (180–240°C ±5°C) | Single heating mode, ±15°C accuracy |
II. Innovative Design Highlights
- Modular Water-Cooled Shooter
- Integrated Design: Built-in water circulation keeps nozzle temperature ≤50°C, preventing resin pre-curing.
- Quick-Split Modification: Split into dual independent shooters in ≤5 mins, compatible with core boxes (Φ50–300 mm).
- Cost Efficiency: Retrofit cost reduced by 70%, compatibility expanded by 300% (supports complex/miniature cores).
- Smart Process Management
- Digital presets for shooting time, pressure holding, and heating curves, improving mold-change efficiency by 90%.
- Self-diagnostic system (covers 12 common faults, e.g., sand clogging, temperature deviations).
III. Shell Core Production Workflow (Phenolic Resin Sand Example)
Step | Parameters | Mechanism |
---|---|---|
1. Core Box Preheating | Initial temp: 200–220°C (electric mode) | Ensures rapid resin melting on core box surface to form a bonding layer. |
2. Sand Injection | Pressure: 0.6 MPa, duration: 5–15 sec | High-pressure airflow ensures ≥98% filling rate (no dead zones). |
3. Shell Formation | Static heating: 30–90 sec (5–12 mm thickness) | Resin near walls carbonizes, bonding sand into dense shell; excess sand automatically discharged (recovery rate >85%). |
4. Curing & Cooling | Air/water cooling to ≤80°C | Prevents thermal deformation, reduces demolding time to <20 sec. |
5. Automatic Ejection | Hydraulic ejector precision: ±0.1 mm | Damage-free demolding, surface roughness Ra ≤6.3 μm (no post-processing). |
IV. Typical Applications & Cost-Benefit Analysis
Industry | Applications | Efficiency Gain | Cost Savings |
---|---|---|---|
Automotive | Engine water jacket cores, turbo housings | 1,200–1,500 pcs/shift (+40% YoY) | 25% less sand, 18% lower energy |
Pump/Valve | Complex-flow valve cores, pressure-resistant pump shells | Yield rate: 88% → 96% | 70% fewer labor dependencies |
Aerospace | Thin-wall turbine blades, superalloy cores | Cycle time: 45 sec (vs. 180 sec) | 90% less post-processing time |
V. Technical Q&A (Common Issues & Solutions)
- Issue 1: Uneven shell thickness due to inconsistent sand injection
Solution: Calibrate shooter-core box alignment (tolerance <0.05 mm); add real-time sand moisture monitoring (target: 3.2–3.8%).
- Issue 2: Demolding adhesion
Solution: Apply nano-coated release agent (1 spray/10k cycles); install vibration-assisted ejection (50 Hz frequency).
This version emphasizes quantifiable metrics, competitive advantages, and industry-specific ROI. Let me know if further customization or additional data is required!
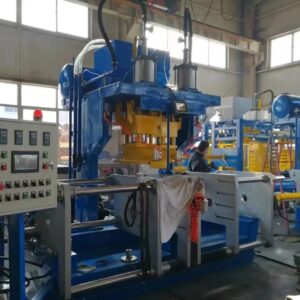
Automatic Core Shooter Product Paramenters
Item/Model | ZH6510 | ZH6520 | ZH6530 | ZH6540 |
Pattern size | 540x400mm | 620x280mm | 620x420mm | 700x450mm |
Clamping stroke | 400mm | 400mm | 400mm | 400mm |
Max sand core weight | 12kg | 20kg | 18kg | 30kg |
Shooting pressure | 0.3-0.4Mpa | 0.3-0.4Mpa | 0.3-0.4Mpa | 0.3-0.4Mpa |
Heat power | 25kw | 25kw | 25kw | 40kw |
automatic core shooter Features:
- High Production Efficiency: The core-making process is quick and simultaneous with sand compaction, allowing for rapid core formation—cycles take as little as 10 to 30 seconds.
- High-Quality Sand Cores: The machine can produce precise, smooth sand cores with accurate dimensions, reducing the need for post-casting finishing.
- Eliminates Auxiliary Equipment: The process eliminates the need for core drying furnaces, dryers, core bones, or wax wires, reducing equipment costs.
- Reduces Labor Intensity: Flexible operation with electric heating, automatic temperature control, and easy cleaning, improving workplace conditions and enabling greater automation.
This core-shooting machine streamlines the core-making process, improving efficiency, product quality, and cost-effectiveness in foundry operations.
Daily Maintenance Measures for automatic core shooter:
- Check for Leaks: Inspect gas cylinders, gas lines, and valves for leaks, addressing any issues promptly.
- Clean Moving Parts: Regularly clean contact surfaces of moving components such as guide bushes and guide posts to ensure smooth operation.
- Tighten Fasteners: Frequently check all bolts and nuts for looseness and tighten them as needed to maintain equipment stability.
- Daily Cleaning: Clean the equipment at the end of each workday. Perform a thorough cleaning of both the interior and exterior of the machine once a week.
- Maintain Cleanliness of Electrical Components: Keep the electrical cabinet and operator interface clean. Ensure the cabinet door is securely closed when not under maintenance or after set times.
By following these maintenance measures, the core shooter will operate efficiently and reliably, extending its lifespan and minimizing downtime.
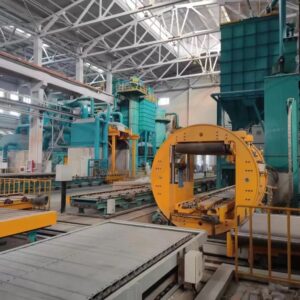
Resin Sand Molding Production Line
Foundry Machinery: China Resin Sand Reclamation Casting Machines
The resin sand molding and core-making process utilizes sand mixed with a specific amount of resin glue, which hardens naturally within a certain timeframe at room temperature. This self-hardening sand technology is widely adopted in modern foundries, with commonly used types including furan resin sand, ester-hardening alkaline phenolic resin sand, and pep-set resin sand.
Key Features:
- Self-Hardening Technology: The molding and core sand harden naturally at room temperature, with the hardening rate and final hardness influenced by ambient temperature and humidity.
- Versatile Applications: Ideal for single-piece production, small batch runs, and various medium to large-scale castings.
- Industry Usage: Widely employed in industries such as general machinery, heavy equipment, shipbuilding, locomotive manufacturing, and motorcycles.
The resin sand molding process offers excellent adaptability and is well-suited for creating high-quality molds and cores for complex castings.
Main Configuration of Simple Sand Treatment System
Key Equipment for Simple Furan Resin Sand Treatment:
- Magnetic Separation Belt Conveyor
- Vibration Crusher
- Bucket Elevator
- Eddy Current Regenerator
- Powerful Flow Curtain Winnowing Device
- Garden Vibrating Screen
- Pneumatic Gate
- Double-Arm Continuous Sand Mixer
- Pulse Dust Collector
- Centrifugal Fan for Dust Collector
Resin Sand Molding & Treatment Equipment:
- S25 Series Sand Mixer
- S28 Series Mobile Sand Mixer
- L12 Series Vibration Shakeout Machine
- ZP Series Sand Crusher
- SZJ Series Old Sand Reclaimer
- Sand Cooling Equipment
- Sand Transportation Equipment
- Environmental Protection Dust Removal Equipment
Our Services & Strength
1. Pre-Payment Services:
- Consultation: Free advice on selecting the most suitable machine.
- Custom Design: Tailored designs for individual requirements.
- Factory Visit: Welcoming tours of our manufacturing facility.
2. After-Sales Service:
- On-Site Commissioning: Engineers/technicians dispatched for setup and training.
- Technical Support: Free ongoing support and reasonably priced spare parts.
3. Guarantee Period:
- Duration: One year.
- Coverage: Full support for issues arising from design flaws or machine quality.
- On-Site Repairs: Technician visits covered by the seller for serious issues.
4. Payment Terms:
- 30% deposit upfront.
- 70% balance before delivery.
5. Lead Time:
- In Stock: Delivery in 10–30 days.
- Out of Stock: Delivery in 20–45 days based on order quantity.
Packaging & Shipping
- Packaging: Plastic film wrapping and plywood wooden cases, customized per client request.
- Transport: Secure container shipping for global delivery.
Our streamlined sand treatment solutions ensure efficiency, reliability, and environmental responsibility, catering to the evolving needs of modern foundries.