Metal Casting Machinery
Your Partner for Precision and Efficiency
1. Introduction to Metal Casting Machinery
Metal casting machinery forms the backbone of modern manufacturing, enabling the transformation of molten metals into intricate components. From automotive parts to aerospace components, these machines combine traditional techniques with cutting-edge technologies like automated die casting and 3D sand printing.
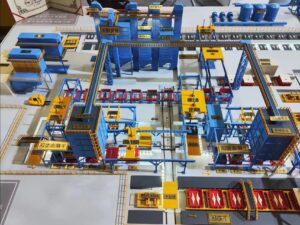
2. Key Types of Metal Casting Equipment
a) Die Casting Machines
Ideal for high-volume production, die casting machines use reusable molds to create lightweight, complex parts (e.g., aluminum engine blocks). Advanced variants integrate real-time pressure sensors to minimize defects.
b) Sand Casting Equipment
A cost-effective solution for large or custom parts. Modern systems employ robotic mold handling and eco-friendly binders to enhance efficiency and reduce environmental impact .
c) Investment Casting Systems
Perfect for precision components like turbine blades. These systems use wax patterns and ceramic molds, achieving tolerances as tight as ±0.1mm .
d) Continuous Casting Machines
Widely used in steel production, they convert molten metal into slabs or billets with minimal waste, leveraging electromagnetic stirring for uniform microstructure 5.
3. Innovations Driving the Industry
- AI-Powered Quality Control: Machine learning algorithms detect micro-cracks and porosity in real-time, reducing scrap rates by up to 30% 5.
- Hybrid Additive Manufacturing: Combining 3D printing with traditional casting to produce hybrid molds with internal cooling channels 11.
- Energy-Efficient Furnaces: Induction furnaces with smart temperature control cut energy consumption by 25% while maintaining metal purity 15.
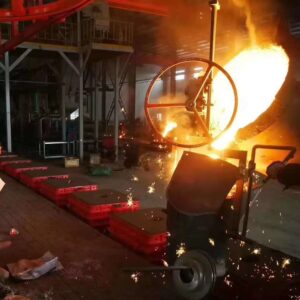
4. Applications Across Industries
Industry | Use Case | Machinery Type |
---|---|---|
Automotive | Engine blocks, transmission parts | High-pressure die casting |
Aerospace | Turbine blades, structural frames | Investment casting |
Construction | Pipes, valves | Sand casting |
Consumer Goods | Jewelry, cookware | Vacuum casting |
5. Future Trends to Watch
- Nanocomposite Molds: Extending mold lifespan by 50% through graphene-reinforced materials 4.
- Decentralized Mini-Foundries: Compact, IoT-enabled systems for on-demand production in small workshops 11.
- Carbon-Neutral Casting: Hydrogen-powered melting furnaces and recycled sand systems achieving net-zero emissions 5.
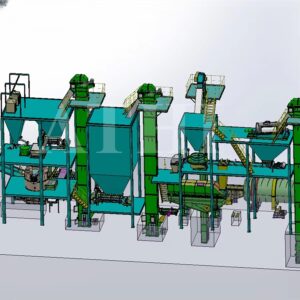
Conclusion
Metal casting machinery is no longer just about pouring molten metal—it’s a synergy of robotics, AI, and sustainable practices. Whether you’re a hobbyist with a home foundry 11 or an industrial manufacturer, embracing these innovations ensures competitiveness in a rapidly evolving market.
Ready to upgrade your foundry? Explore our curated selection of advanced metal casting solutions and request a personalized consultation today!