Lost Wax Metal Casting Equipments
Precision Tools for Complex Component Manufacturing
Introduction
Lost wax metal casting, an ancient technique refined for modern industry, relies on advanced equipment to produce intricate, high-tolerance metal components. At KW Casting, our lost wax metal casting equipments integrates cutting-edge automation, IoT connectivity, and precision engineering to meet the demands of aerospace, medical, and luxury manufacturing. This article explores how our systems streamline the entire wax-to-metal workflow while minimizing waste and maximizing ROI.
Essential Equipment for the Lost Wax Casting Process
1. Wax Pattern Fabrication
- High-Pressure Wax Injection Machines:
- Deliver ±0.02mm accuracy for complex geometries like turbine blades or dental implants.
- AI-adjusted temperature control (70–130°C) for stable wax flow with minimal shrinkage.
- Rapid Prototyping Tools:
- 3D-printed wax molds enabling 48-hour turnaround for design validation.
2. Ceramic Shell Production
- Robotic Dip Coating Systems:
- Apply uniform slurry layers with viscosity sensors and automated stucco application.
- Compatible with zircon, fused silica, and alumina refractories.
- Smart Drying Ovens:
- Multi-zone humidity control (40–70% RH) to prevent shell cracking during curing.
3. Metal Melting & Pouring
- Vacuum Induction Furnaces:
- Melt superalloys (Inconel 718, Titanium 6Al-4V) under inert atmospheres to prevent oxidation.
- Tilt-Pour Systems:
- Ensure laminar flow for thin-walled castings in aerospace or automotive parts.
4. Post-Casting Finishing
- Automated Deburring Cells:
- Robotic grinding and polishing for Ra <0.4µm surface finishes.
- Non-Destructive Testing (NDT) Stations:
- X-ray and CT scanning to detect internal defects without damaging components.
Lost Wax Metal Casting Equipments
- X-ray and CT scanning to detect internal defects without damaging components.
Technological Breakthroughs in Modern Lost Wax Equipment
1. IoT-Enabled Process Control
- Real-time monitoring of wax injection pressure, furnace temperatures, and shell drying rates via cloud-based dashboards.
- Predictive maintenance alerts reduce unplanned downtime by 40%.
2. Hybrid Energy Efficiency
- Regenerative burners in furnaces and heat recovery in ovens cut energy costs by 30%.
- Solar-compatible power systems for sustainable foundries.
3. AI-Driven Defect Prevention
- Machine learning algorithms analyze historical data to optimize wax injection parameters and reduce scrap rates by up to 50%.
Industry Applications: Precision Meets Innovation
- Aerospace: Produce single-crystal turbine blades with internal cooling channels.
- Medical: FDA-compliant cobalt-chrome orthopedic implants with biocompatible surfaces.
- Jewelry: Micro-casting equipment for intricate platinum or gold designs.
- Automotive: High-volume production of aluminum EV motor housings with near-net shapes.
How to Choose Lost Wax Casting Equipment
Selecting the right precision lost wax casting equipment requires evaluating:
- Material Compatibility: Supports wax alloys, ceramics, and metals (e.g., stainless steel, titanium).
- Production Scale: Batch vs. continuous workflows (e.g., 100 vs. 10,000 units/month).
- Certifications: NADCAP, ISO 9001, or AS9100 compliance for regulated industries.
- Automation Level: Robotic integration for lights-out manufacturing.
Pro Tip: Prioritize modular systems like KW Casting’s FlexiCast Pro Series for adaptability to future design changes.
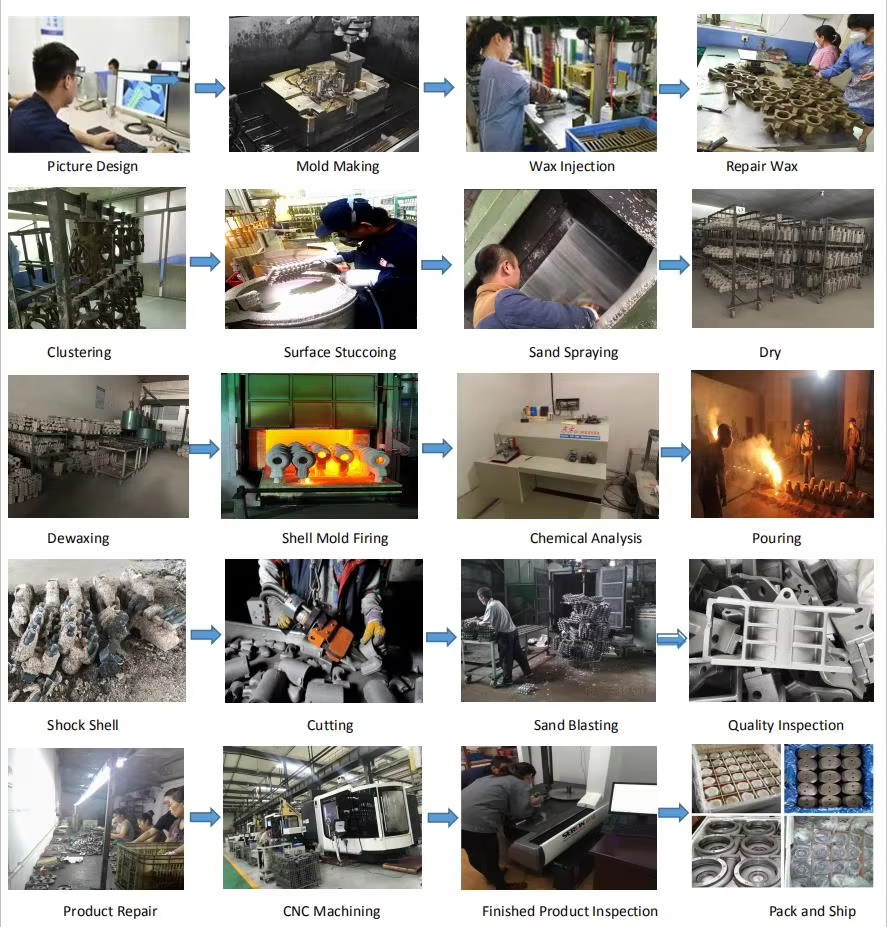
KW Casting’s Competitive Edge
As a leader in industrial lost wax equipment manufacturing, we offer:
✅ End-to-End Solutions: From wax injection to final heat treatment.
✅ 5-Year Performance Warranty: Guaranteed uptime and technical support.
✅ Custom Configurations: Tailored clamping forces (20–500 tons), furnace sizes, and automation levels.
Download Our Lost Wax Equipment Catalog
Case Study: Boosting Efficiency for a Turbine Manufacturer
A client producing Inconel turbine vanes faced 20% scrap rates due to wax distortion and shell cracks. KW Casting implemented:
- AI-Optimized Wax Injectors: Adjusted pressure profiles in real time.
- Vacuum Shell Drying Ovens: Eliminated moisture-induced defects.
Result: Scrap rates dropped to 4%, saving $650K annually.
Conclusion
Investing in advanced lost wax metal casting equipment is essential for mastering complex, high-value component production. Partner with KW Casting to access technology that aligns with AMS 2175, ASTM E606, and other stringent standards. Contact us for a free process audit and customized ROI analysis.
Keywords:
- Lost wax metal casting equipment
- Precision lost wax casting tools
- Wax injection systems for investment casting
- Ceramic shell coating machines
- Vacuum melting furnaces
- Automated deburring equipment
- Aerospace-grade casting tools
- NADCAP-certified foundry systems
Call to Action:
Upgrade Your Casting Capabilities Today!