Setting Up a Lost Wax Casting Workshop
A Comprehensive Guide for Industrial Manufacturing
A lost wax casting workshop is a cornerstone of modern industrial manufacturing, enabling the production of high-precision components such as motor housings, pump casings, and machine parts. At Kewei Casting Machinery, we understand the complexities of setting up and optimizing such a workshop. This guide will walk you through the essential steps, equipment, and best practices to establish a highly efficient lost wax casting operation.
What is a Lost Wax Casting Workshop?
A lost wax casting workshop is a specialized facility where intricate metal parts are produced using the investment casting process. This method involves creating a wax model, coating it with ceramic, and then melting the wax to form a mold for metal casting. The result is a highly accurate and detailed final product, ideal for industrial applications.
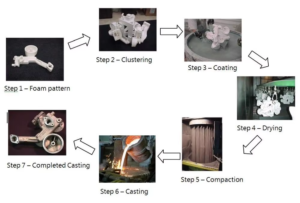
Key Components of a Lost Wax Casting Workshop
- Wax Injection Machines
- Used to create precise wax patterns.
- Essential for maintaining the accuracy of the final cast.
- Shell Building Systems
- Apply ceramic slurry to wax patterns.
- Ensure the mold can withstand high temperatures during metal pouring.
- Dewaxing Autoclaves
- Remove wax from the ceramic shell.
- Critical for preparing the mold for metal casting.
- Melting and Pouring Systems
- Melt metal and pour it into the mold.
- Must be capable of handling various metals, including stainless steel and aluminum.
- Finishing Equipment
- Includes grinders, polishers, and CNC machines for final touches.
- Ensures the final product meets exact specifications.

Steps to Set Up a Lost Wax Casting Workshop
- Planning and Design
- Assess your production needs and space requirements.
- Design the layout to optimize workflow and minimize material handling.
- Selecting Equipment
- Choose machines that match your production volume and material types.
- Ensure compatibility between different pieces of equipment.
- Installation and Calibration
- Properly install and calibrate all machines.
- Conduct initial tests to ensure everything is functioning correctly.
- Training and Safety
- Train staff on operating procedures and safety protocols.
- Implement safety measures to protect workers from high temperatures and hazardous materials.
- Quality Control
- Set up a quality control system to monitor production.
- Regularly inspect equipment and final products to maintain high standards.
Applications of a Lost Wax Casting Workshop
- Motor Housings: Produce durable and precise housings for electric motors.
- Pump Casings: Create complex geometries for efficient fluid handling.
- Machine Parts: Manufacture high-strength components for industrial machinery.
- Aerospace Components: Fabricate lightweight and durable parts for aircraft.
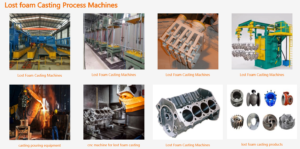
Why Choose Kewei Casting Machinery?
At Kewei Casting Machinery, we provide state-of-the-art equipment and expert guidance to help you set up and optimize your lost wax casting workshop. Our solutions are designed for:
- High Precision: Achieve tolerances as tight as ±0.05mm.
- Durability: Built to withstand the rigors of high-volume production.
- Customization: Tailored solutions to meet your specific needs.
Conclusion
Setting up a lost wax casting workshop is a significant investment that can greatly enhance your manufacturing capabilities. By following this guide and partnering with Kewei Casting Machinery, you can ensure a smooth setup process and achieve exceptional results. Ready to take your production to the next level? Contact us today to explore our range of equipment and services.
Transform your manufacturing process with Kewei’s lost wax casting solutions. Request a free consultation today and get a customized quote!