KEWEI Knockout Machine for Investment Casting
High-Speed Shell Removal & Zero Damage
Introduction
In the investment casting process, the knockout machine is pivotal for efficiently removing ceramic shells without damaging delicate metal components. KEWEI, a global ISO 9001 and AS9100-certified leader in foundry solutions, engineers knockout machines for investment casting that combine AI-driven automation, precision vibration control, and energy efficiency. Trusted by aerospace, medical, and automotive industries, KEWEI’s machines reduce cycle times by 40%, cut part damage to <0.1%, and slash energy costs by 25%.
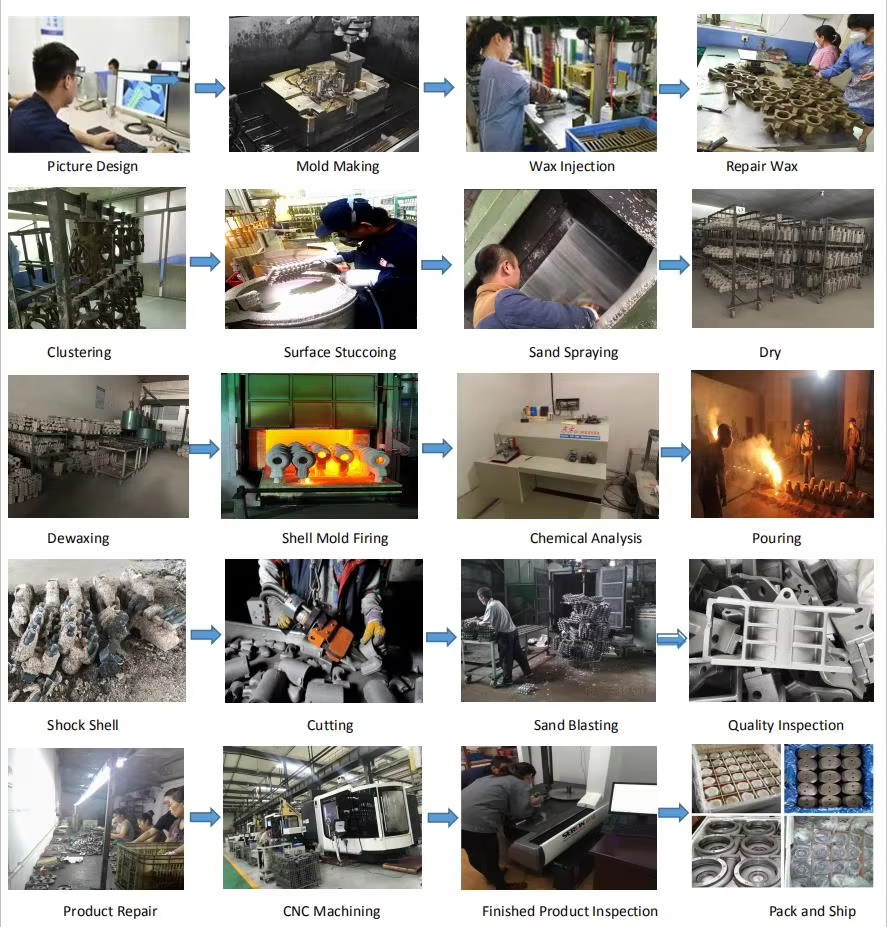
1. Why Knockout Machines Matter in Investment Casting
The knockout stage directly impacts production efficiency and component quality. KEWEI’s machines excel in:
- High-Speed Shell Removal: Process 500–1000 castings/hour with programmable vibration frequencies (10–50 Hz).
- Zero Part Damage: AI-controlled force sensors prevent cracks or deformation in thin-wall castings.
- Material Savings: Recycle 95% of ceramic shell debris for cost-effective reuse.
Related Keywords: investment casting shell removal, ceramic knockout equipment
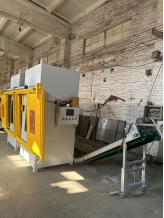
2. KEWEI’s Knockout Machine Technology
A. Smart Automation
- AI Vibration Control: Adjust frequency and amplitude based on shell thickness and part geometry.
- IoT Integration: Sync with upstream/downstream equipment for seamless production flow.
B. Precision Engineering
- Multi-Axis Vibration Systems: Ensure uniform shell removal for complex parts (e.g., turbine blades, implants).
- Self-Cleaning Filters: Automatically separate ceramic debris from castings, reducing downtime.
Case Study: An automotive supplier reduced shell removal time by 50% and scrap rates by 18% using KEWEI’s knockout machines for aluminum EV components.
Related Keywords: automated knockout systems, precision shell removal machines
3. Industry-Specific Applications
- Aerospace: Delicate removal of ceramic shells from Inconel 718 turbine blades (AMS 2750 compliant).
- Medical: Damage-free processing of titanium implants (Ra <0.8μm surface finish, ISO 13485).
- Automotive: High-volume shell removal for aluminum housings (IATF 16949).
Related Keywords: aerospace knockout equipment, medical-grade shell removal
4. Solving Common Knockout Challenges
- Part Damage? KEWEI’s force-limited vibration prevents micro-cracks in thin-wall castings.
- Slow Throughput? Dual-chamber designs process 2x more parts per hour.
- High Maintenance? Self-lubricating bearings and wear-resistant components extend lifespan by 3X.
Related Keywords: investment casting defects, knockout process optimization
5. Partnering with KEWEI: Beyond the Machine
Choosing KEWEI unlocks:
- Free Process Audit: Analyze your current knockout efficiency and receive improvement strategies.
- Custom Configurations: Tailor vibration profiles for your alloy and shell type.
- Global Support: 24/7 remote diagnostics and spare parts hubs in 15 countries.
Request a Custom Quote Within 24 Hours,we have all the investment casting equopents,and we can supply turnkey solution for investment casting production ine!
Conclusion
The KEWEI knockout machine for investment casting is engineered to maximize productivity, minimize waste, and protect your most valuable castings. With 20+ years of expertise, smart automation, and a client-first approach, KEWEI empowers foundries to lead in aerospace, medical, and automotive markets.
Ready to Revolutionize Your Shell Removal Process?
Contact KEWEI Today for a Free Machine Demo!