Investment Casting Process Equipments
Comprehensive Solutions for End-to-End Excellence
Introduction
Investment casting process equipment forms the backbone of precision metal component production, bridging design intent to flawless execution. At KW Casting, we engineer turnkey investment casting equipments that optimizes every stage of the lost-wax process—from wax pattern creation to final finishing. This guide explores how our integrated systems empower foundries to meet aerospace, medical, and automotive standards while reducing operational costs.
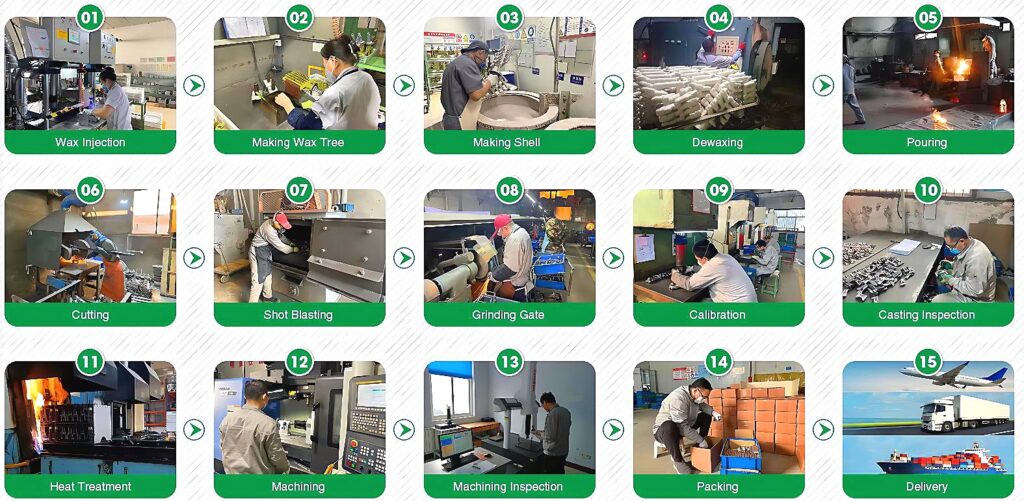
Core Equipment in the Investment Casting Workflow
1. Wax Pattern Production
- Precision Wax Injection Machines:
- High-pressure (8–20 MPa) systems for zero-defect patterns with ±0.03mm tolerances.
- AI-driven temperature control for hybrid wax blends (synthetic, vegetable-based).
- Rapid Tooling Systems:
- Modular CNC-machined molds enabling fast design iterations for prototypes.
2. Ceramic Shell Building
- Automated Dip Coating Systems:
- Robotic slurry applicators with viscosity sensors for uniform refractory layers.
- Stucco sanding units optimized for zirconia or fused silica materials.
- Drying & Curing Ovens:
- Multi-zone humidity control (30–70% RH) to prevent shell cracking.
3. Melting & Pouring
- Vacuum Induction Melting (VIM) Furnaces:
- Melt superalloys (Inconel, Titanium) at 1,600°C+ with <10 ppm oxygen levels.
- Tilt-Pour Systems:
- Minimize turbulence for thin-wall castings in aerospace components.
4. Post-Casting Processing
- Shot Blasting Machines:
- Remove ceramic shell residues without damaging delicate surfaces.
- CNC Finishing Centers:
- Achieve Ra <0.8µm finishes for medical implants or turbine blades.
How Advanced Equipments Reduces Defects by 50%
Modern investment casting machinery integrates smart technologies to tackle critical challenges:
- Wax Distortion: Real-time thermal monitoring in ovens ensures uniform cooling.
- Shell Porosity: AI-adjusted slurry viscosity eliminates air entrapment.
- Dimensional Inaccuracy: Laser-guided alignment in CNC machines guarantees ±0.05mm compliance.
KW Casting’s IoT-enabled equipment provides predictive maintenance alerts, cutting downtime by 35%.
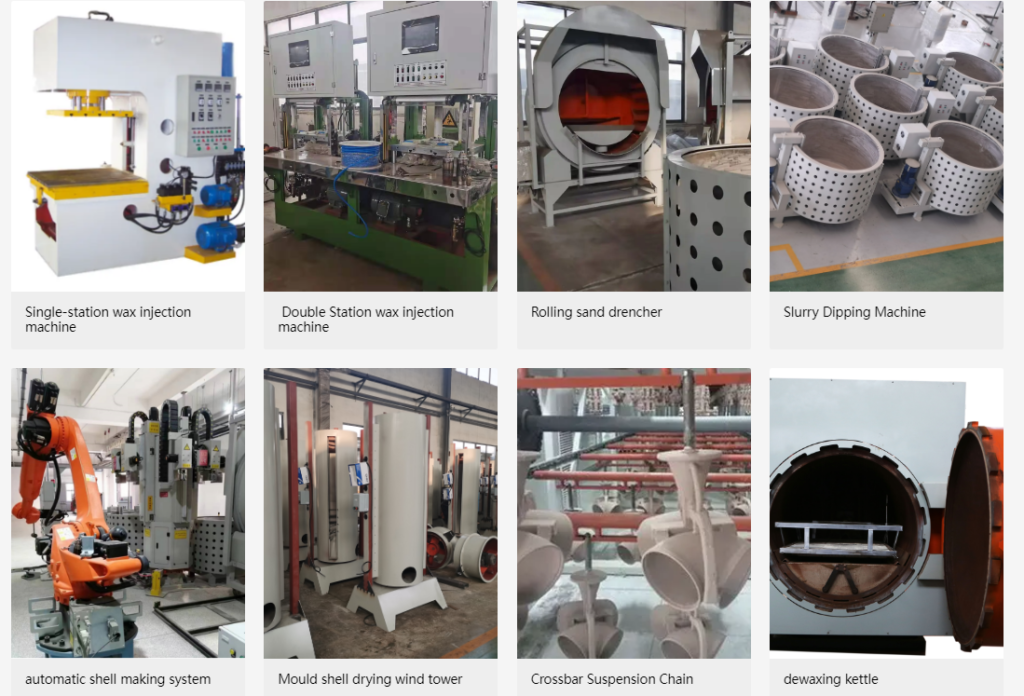
Industry-Specific Equipment Configurations
- Aerospace:
- Vacuum melting furnaces + robotic shell coating for single-crystal turbine blades.
- Medical:
- Micro-wax injection machines + electropolishing systems for FDA-grade implants.
- Automotive:
- High-speed wax printers + automated grinding cells for EV motor housings.
Key Considerations When Selecting Investment Casting Equipment
Evaluate systems based on:
- Production Scale: Batch vs. continuous workflows.
- Material Compatibility: Aluminum, steel, or nickel-based superalloys.
- Automation Level: Semi-automatic vs. fully robotic integration.
- Certifications: NADCAP, ISO 9001, or AS9100 compliance.
Pro Tip: Prioritize modular designs (e.g., KW Casting’s FlexiCast Series) to future-proof your foundry.
KW Casting’s Equipment Advantages
As a leader in industrial casting equipment manufacturing, we deliver:
✅ End-to-End Integration: Seamless compatibility between wax, shell, and melting systems.
✅ Energy Efficiency: Heat recovery systems reduce power costs by 25–40%.
✅ Global Support: 24/7 remote diagnostics and on-site technicians in 20+ countries.
Explore Our Equipment Portfolio
Case Study: Revolutionizing a Turbine Component Foundry
A client producing Inconel 718 turbine seals faced 15% scrap rates due to shell cracks and wax defects. KW Casting’s solution:
- Upgraded Wax Injection Machines: Implemented multi-stage pressure control.
- Smart Drying Ovens: Installed humidity-tracking IoT sensors.
Result: Scrap rates dropped to 3%, achieving annual savings of $500K.
Conclusion
Investing in advanced investment casting process equipment is pivotal for meeting today’s quality, speed, and sustainability demands. Partner with KW Casting to access certified, future-ready systems tailored to your production goals. Contact us for a free equipment audit and ROI projection.
Keywords:
- Investment casting process equipment
- Precision casting machinery
- Wax injection systems for foundries
- Ceramic shell coating equipment
- Vacuum melting furnaces
- Automated post-casting systems
- Industrial casting oven solutions
- NADCAP-certified foundry equipment
Call to Action:
Transform Your Foundry Today!