Investment Casting Foundry Equipment
Precision, Automation & Scalability Redefined
In the high-stakes world of precision manufacturing, investment casting foundry equipment is the backbone of producing complex, high-performance metal components. KEWEI, a global ISO 9001 and AS9100-certified leader, delivers full-spectrum foundry equipment that empowers aerospace, automotive, and medical industries to achieve zero-defect production, 30% lower operational costs, and seamless scalability. Discover how KEWEI’s smart, sustainable solutions transform raw materials into market-ready masterpieces.
1. Core Components of KEWEI’s Investment Casting Foundry Equipment
KEWEI’s investment casting foundry equipment covers every critical stage of production:
A. Wax Pattern Systems
- 3D Wax Printers: Achieve ±0.05mm tolerances for intricate geometries (e.g., turbine blades, implants).
- AI-Driven Wax Injectors: Reduce defects by 35% through real-time temperature/pressure control.
B. Ceramic Shell Automation
- Robotic Slurry Coaters: 6-axis arms ensure ±0.1mm shell uniformity.
- Smart Drying Tunnels: Cut curing time by 30% with predictive humidity algorithms.
C. Melting & Pouring Technology
- Vacuum Induction Furnaces: Melt superalloys (Inconel, titanium) up to 1800°C (±3°C stability).
- IoT-Enabled Pouring Robots: Eliminate turbulence defects via adaptive flow control.
D. Post-Casting Solutions
- Automated Knockout Machines: Remove ceramic shells 50% faster with <0.1% part damage.
- 5-Axis CNC Finishers: Achieve Ra <0.8μm for medical-grade surface finishes.
Related Keywords: precision foundry equipment, industrial casting machinery
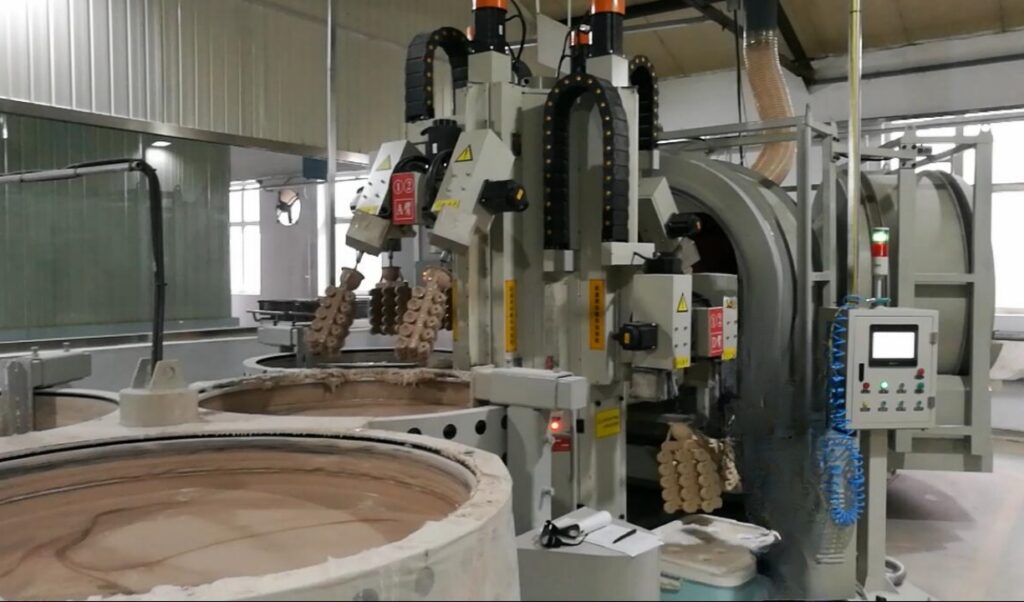
2. KEWEI’s Competitive Edge in Investment Casting Foundry Equipment Technology
A. Smart Factory Integration
- AI-Powered Process Control: Machine learning optimizes parameters for 99.9% defect-free outputs.
- IoT Connectivity: Sync equipment with ERP/MES systems for real-time production tracking.
B. Sustainability & Cost Efficiency
- Energy Recovery Systems: Recapture 85% of furnace heat, cutting power costs by 25%.
- Closed-Loop Recycling: Reuse 95% of ceramic shell materials to reduce waste.
Case Study: A German automotive supplier slashed annual operating costs by $420,000 using KEWEI’s automated foundry line for aluminum EV components.
Related Keywords: energy-efficient foundry equipment, sustainable casting solutions
3. Industry-Specific Solutions
- Aerospace: AS9100-certified vacuum furnaces + 7-axis CNC machines for NASA-spec turbine blades.
- Medical: Cleanroom-compatible systems for FDA-grade titanium implants (ISO 13485).
- Energy: High-pressure shell equipment for API 6A-compliant offshore valves.
Related Keywords: aerospace casting equipment, medical foundry machinery
4. Solving Foundry Pain Points
- High Labor Costs? KEWEI’s robotics handle 80% of repetitive tasks.
- Inconsistent Quality? AI vision inspects 100% of parts for micron-level defects.
- Slow ROI? Achieve breakeven in <18 months via waste reduction and uptime gains.
Related Keywords: foundry equipment optimization, casting process challenges
5. Partnering with KEWEI: End-to-End Support
Choosing KEWEI unlocks:
- Free Facility Audit: Optimize workflow layout for maximum efficiency.
- Turnkey Installation: From equipment setup to staff training.
- Global Warranty: 3-year coverage with 24/7 remote diagnostics.
Request a Custom Quote Within 24 Hours!
Conclusion
KEWEI investment casting foundry equipment is more than machinery—it’s a catalyst for precision, profitability, and planetary responsibility. With 20+ years of innovation, 50+ patents, and a client base across 30 countries, KEWEI empowers foundries to lead in aerospace, medical, and automotive markets.
Ready to Future-Proof Your Foundry?
Contact KEWEI Today or Download Our Catalog for Full Technical Specs!